
Monitoring
NEXPOM plays the role of the main control office in the factory by providing a real-time monitoring function. NEXPOM’s system module is integrated into the current status of the factory based on manufacturing, quality, energy, and facility standards. It also provides an index of optimum factory operations by identifying correlations between data.
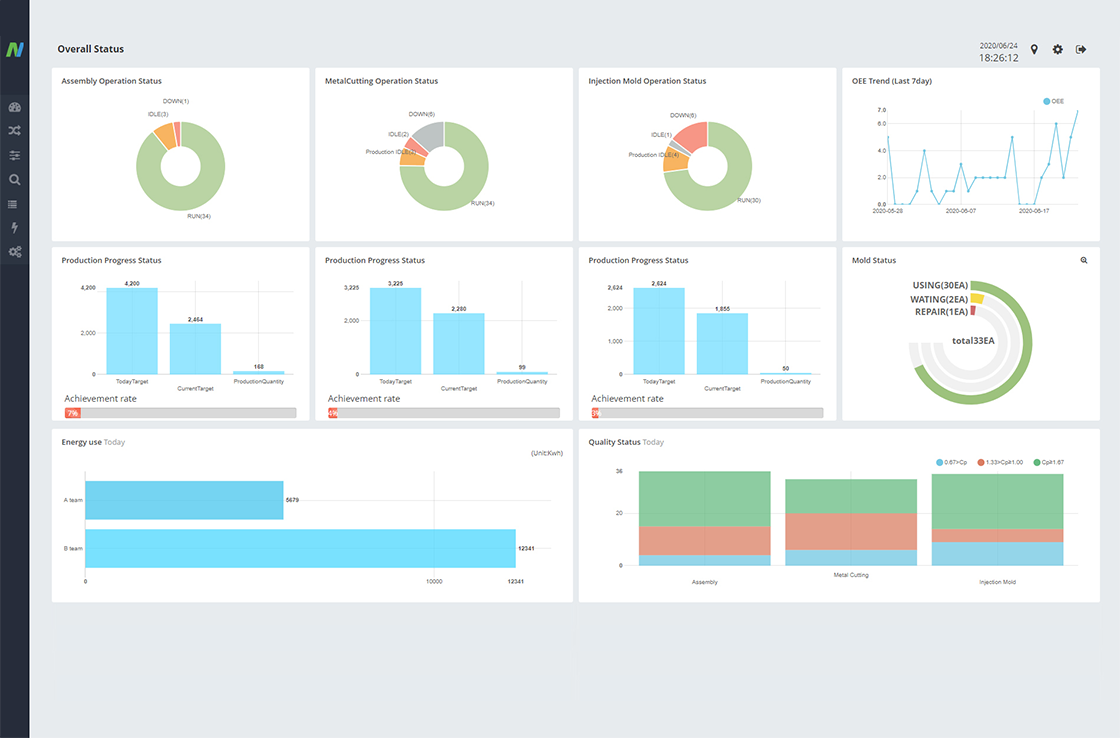
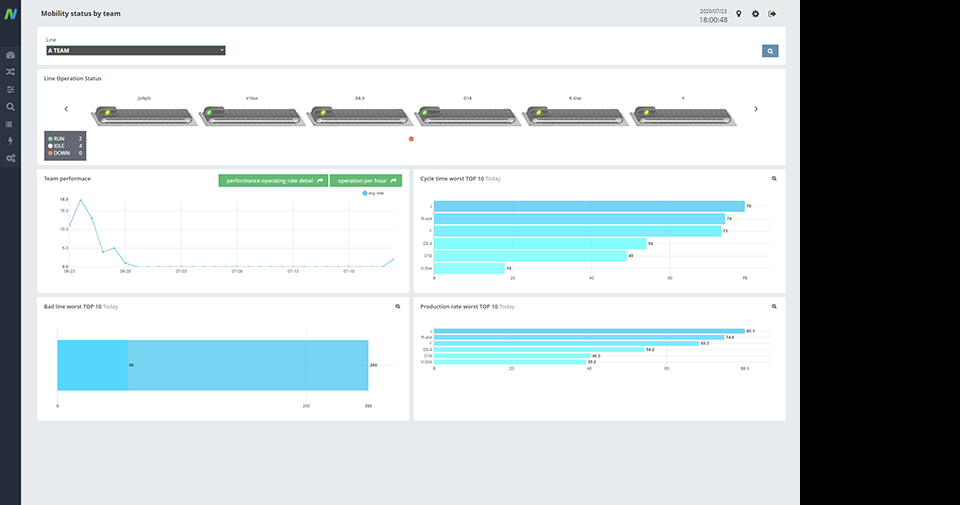
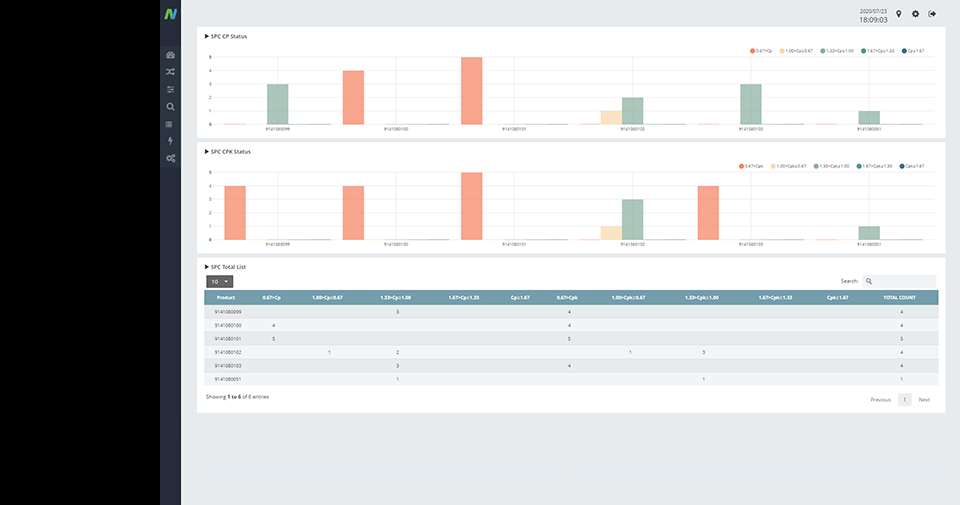
Examples of monitoring utilization
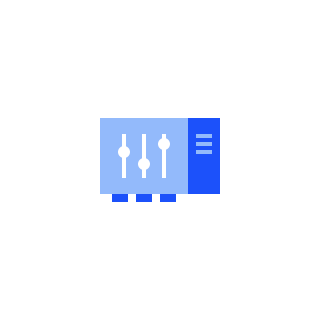
STEP. 1 Data collection and OEE analysis & monitoring through controllers, and PLC I/F of processing facilities
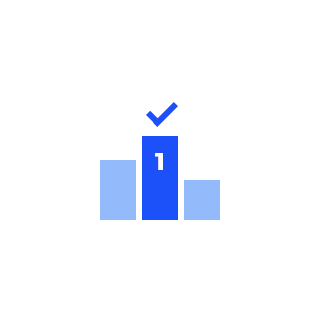
STEP. 2 Prioritization of loss factors by analyzing types, frequencies, accumulated time, etc. of loss factors
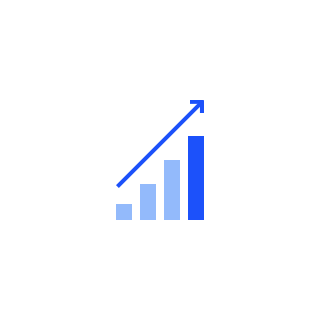
STEP. 3 Achieving improvement of productivity and cost reduction effect by managing and improving higher priority factors
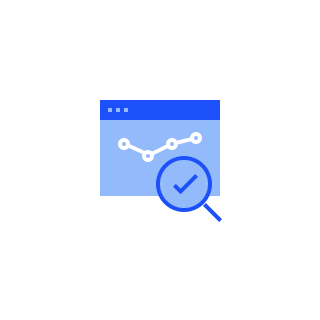
STEP. 4 Using KPI updates through application, analysis, and verification of new scenarios on undefined factors
Use case of monitoring
A company in the field of medical devices
-
Product
Monitoring + MES -
Goal
To establish a smart factory that prepares for managing the quality (UDI) of medical devices that gradually increases and maximizes production efficiency through precise stock management.
Contents
- Lot track management through MES from warehousing to shipment of materials
- Automation of manufacturing data collection through facility I/F
- Precise stock identification and monitoring of raw materials, half-finished products, and complete products
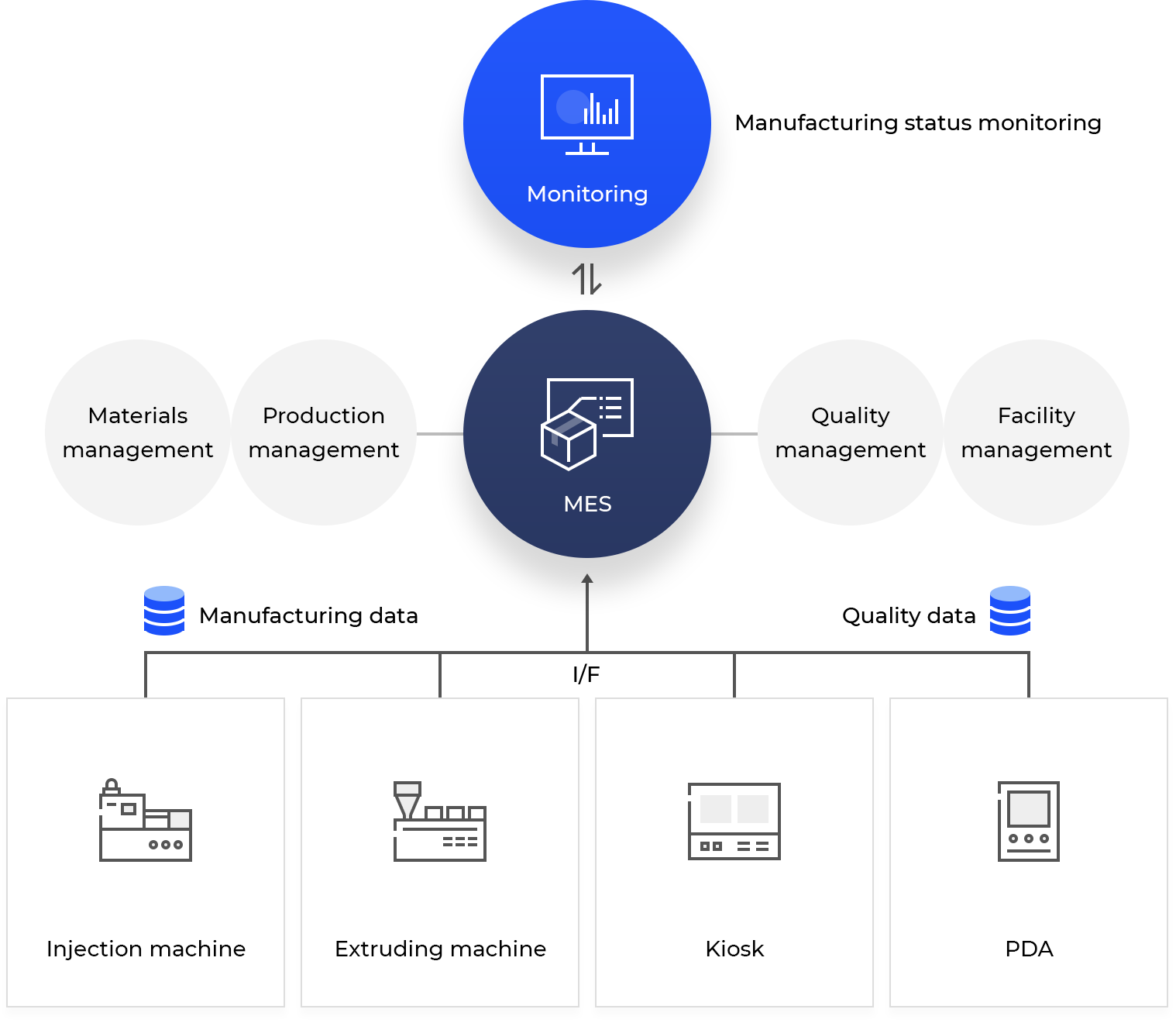
Implementation effects
-
25%
25% increase in output based on an organizational systemization of the manufacturing process
-
24%
24% reduction in defect rate of complete products through real-time management of measurement data
-
4%
4% reduction of stock fees by identifying accurate material quantity demand according to output
-
10%
10% reduction of lead time through precise delivery period prediction based on process status management
Contact us
-
Hyunsun Shin
- hsshin@wizcore.co.kr
- +82-10-9943-9118