
MES
A site-centered manufacturing execution system that can manage the process from materials warehousing to shipment of manufactured products, according to the actual work flow based on manufacturing data.
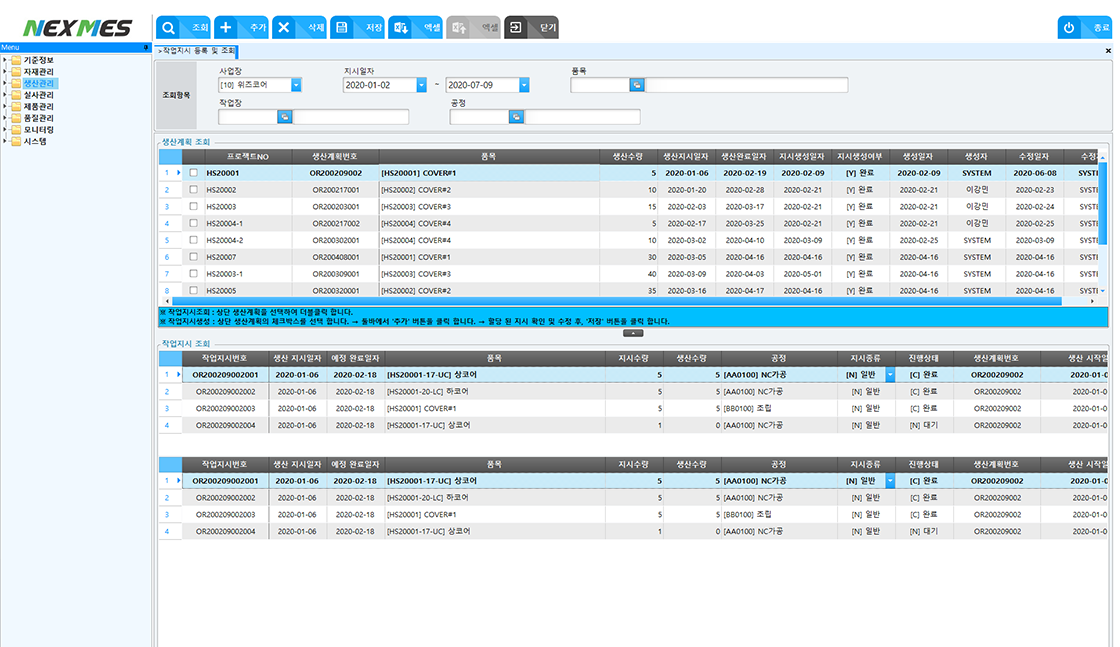
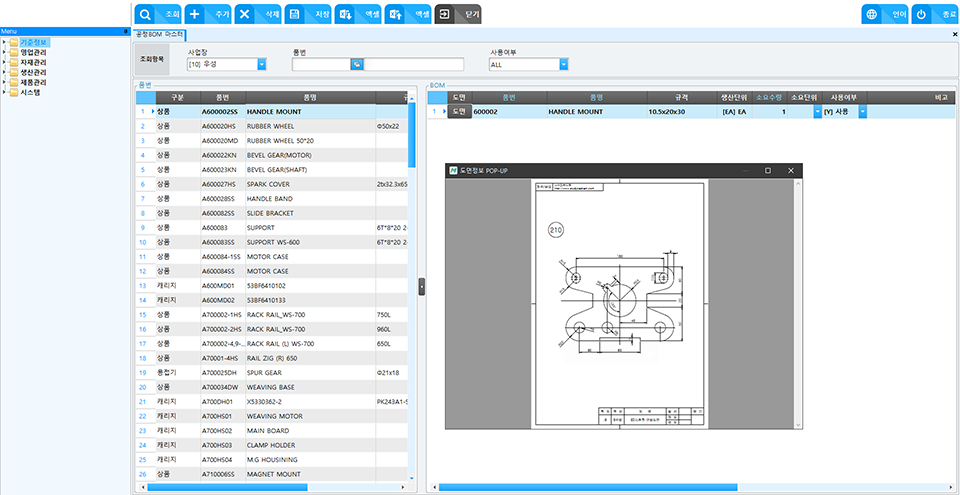
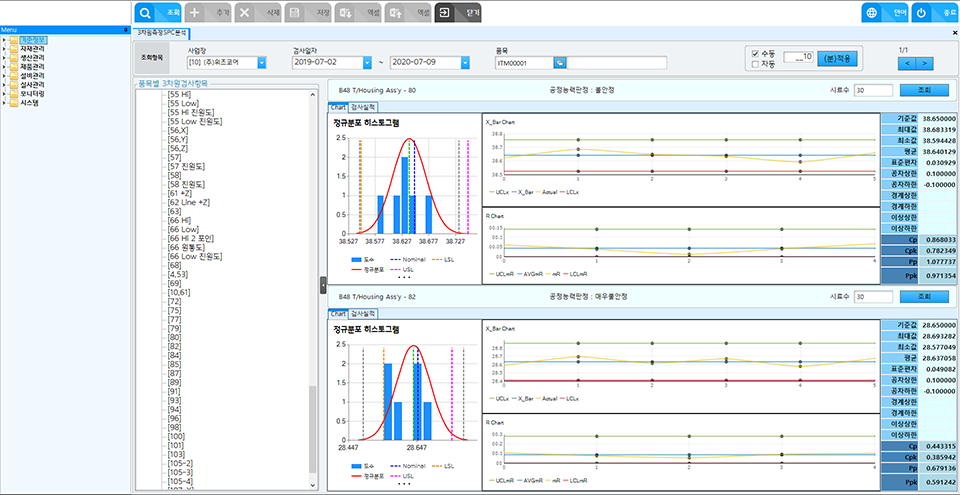
MES can systematically manage all manufacturing processes.
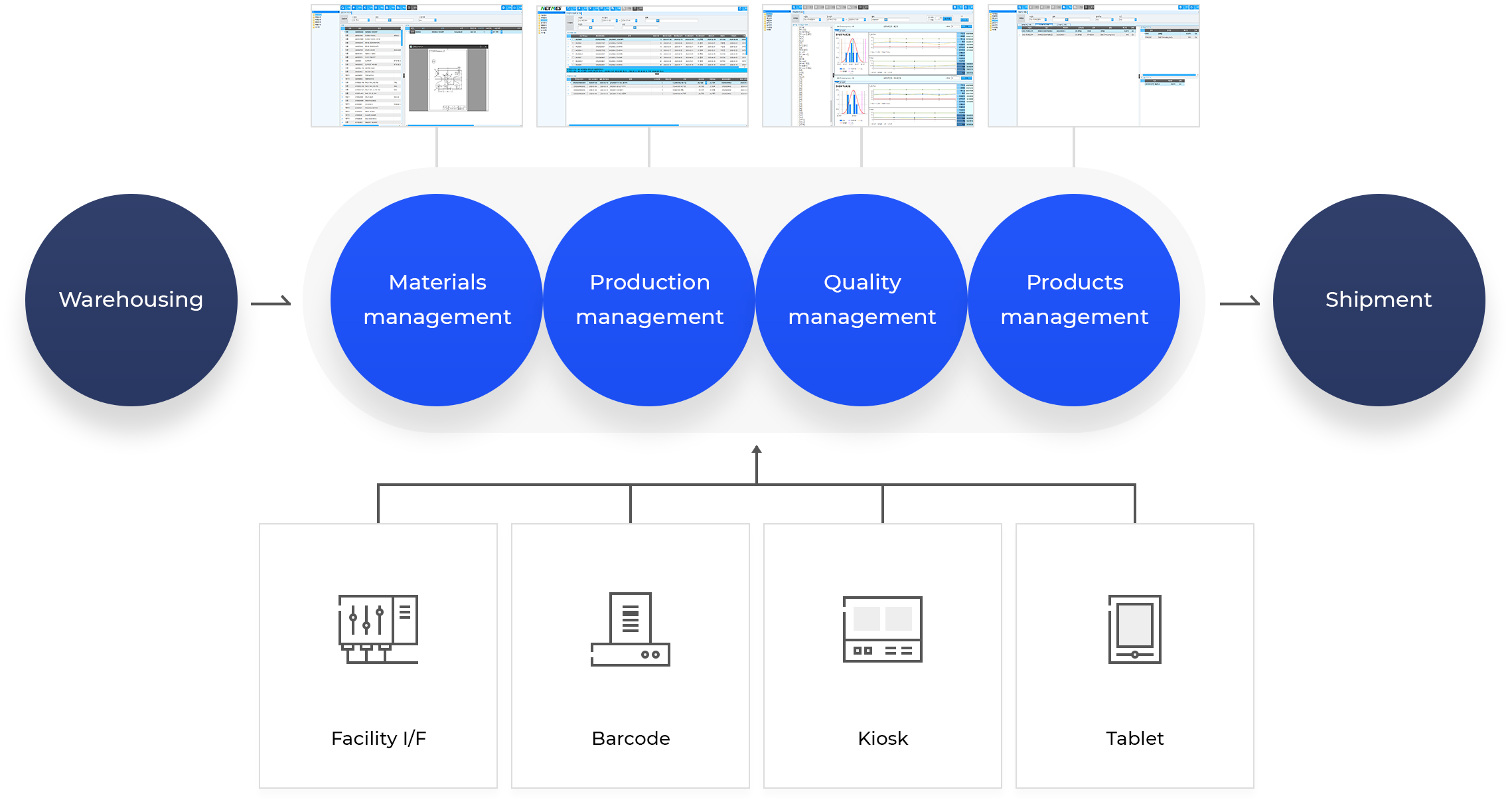
Strong points of MES
-
An actual work flow-based system
Output and work-in-process of providing half-finished products, etc. can be managed at any time through real-time collection of manufacturing performance information.
-
Automation of data collection
As it excludes manual data collection methods and collects data through automatic methods as much as possible, it decreases paperwork, errors, and the mis-entry of data.
-
Process trackable system
Since it can track material input records of products and track processes, it can track the data of the manufactured products and perform a cause analysis on which problems occurred during which processes, which improves the quality of the products.
-
Real-time problem handling
It can perform real-time monitoring and receive alarms when abnormalities occur, so that necessary measures can be taken rapidly to fix system or process abnormalities.
Use case of MES
M company in the field of automobile parts
-
Product
MES -
Goal
Smart factories were established to achieve quality stabilization and customer reliability improvements as a client company of M company requested barcoded content management for quality management.
Contents
- Real-time confirmation of facility operation status through main facility I/F
- Quality data collection and management through a coordinate measuring machine
- Implementation of MES that could integrate into a individual legacy system
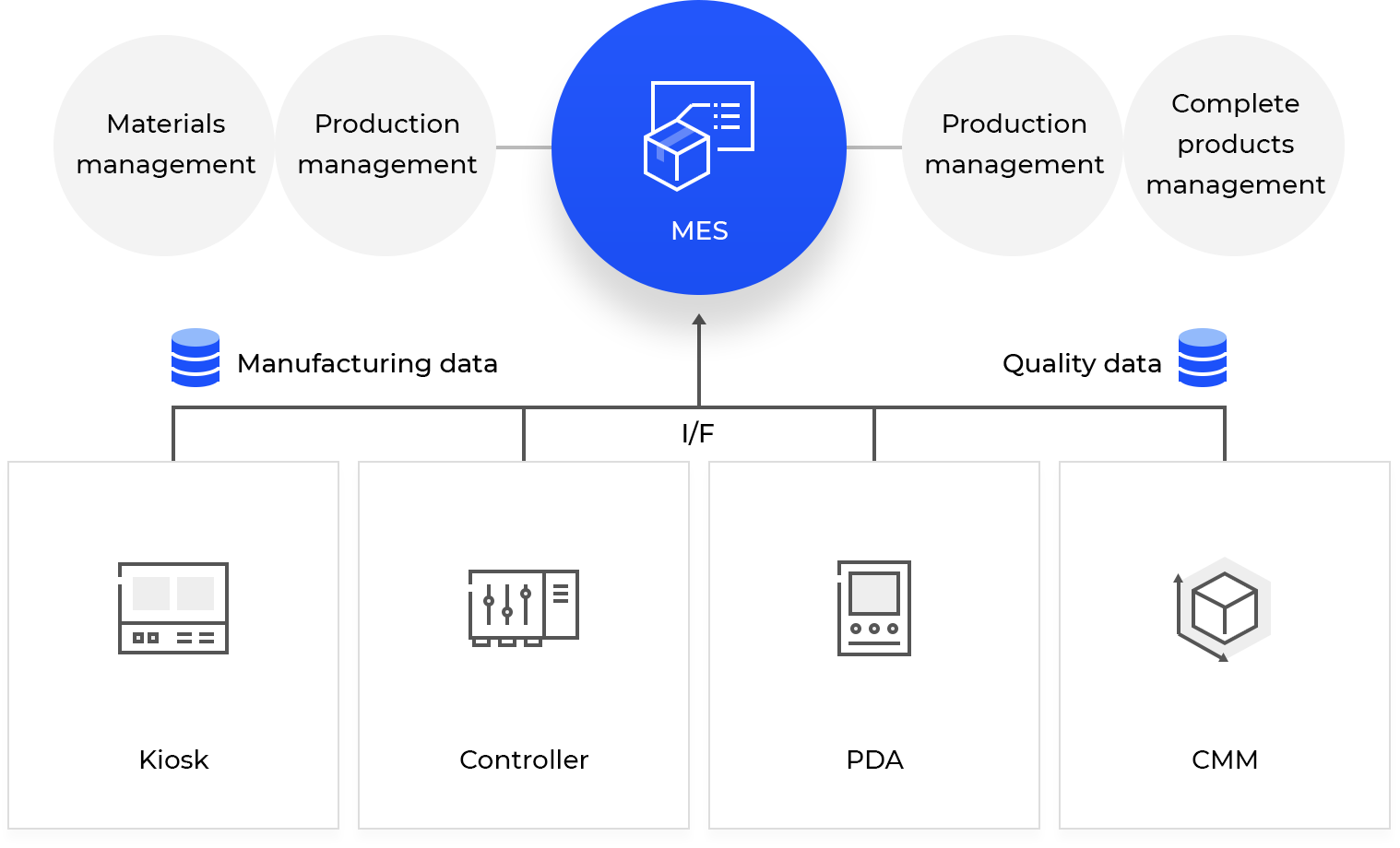
Implementation effects
-
25%
25% reduction of process’ defect rate by real-time quality information collection and analysis management
-
9%
9% increase in output with prompt and consistent manufacturing performance management
-
20%
20% improvement of work-in-progress products through precise manufacturing data collection and management
-
18%
18% increase in facility operation rate through real-time monitoring and management of facility operation status
Contact us
-
Hyunsun Shin
- hsshin@wizcore.co.kr
- +82-10-9943-9118